Product Data Control
PRODUCT DATA CONTROL provides an organized structure for the documentation and maintenance of current and historical configurations on all assemblies in the manufacturing process. Bills of Material are identified as engineering controlled, released to production or both.
Expandable’s unique Data Exception Reporting enhances Bill of Material accuracy. Product Data Control goes beyond the norm by incorporating material planning reports that address component availability (can I build it?). The standard costing system supports the development of new standard costs and the review of their impact on inventory before updating current standard cost.
MODULE FEATURES
Bill of Material Maintenance
- Unlimited annotation of component reference designators
- Browse by assembly or component
- Single level bill display while entering/changing bill of material
Planning Bills of Material
Bill Copy Capability
- Copy entire bill of material, specific type or effective date
- Option to include component references
Bill of Material Viewer
- Drag and drop parts and assemblies from Parts List window onto any component or assembly in BOM View window
- Easily generate BOM from scratch using drag and drop
- Delete selected component(s) or assemblies from a BOM
- Edit BOM with a double click on the component line
- Produce single level cost roll up report from within BOM viewer for estimating and what-if scenarios
Product Structure Provides
- Single level BOM (costed option)
- Indented BOM (costed option)
- Where-used, single level
- Where-used, indented with cumulative lead times
- Option to update cumulative lead time on parts master file
Engineering Data
- Drawing item number
- Annotate component references for revision level and ECN
- Effectivity start and stop dates, serial numbers
Manufacturing Data
- Quantity required up to 6 decimal places
- Default kitting storeroom and deliver to operation
- Lead time offset
- Scrap factor
Component Availability and Shortage List
- Summarized components requirements
- Netted against on-hand inventory, WIP, purchase orders, receipts, kits
- Purchase orders, jobs and kits detailed
- Indented or single level
- Option to report projected shortages only
- Can process multiple assemblies with a priority control code
- Option to explode buy parts
Product Costing
- Build new standards (cost fields to 6 decimals)
- Current vs. new costed stock status reporting
- Roll-up standard costs, all or single assembly
- option to include scrap and/or yield
- roll-up configurations with no bill
- Re-valuation of inventory and cost variance analysis for GL booking
Data Exception Audit Reporting
- Zero cost part, zero lead time part
- Inactive, obsolete or pre-released part in BOM
- Inactive or obsolete part with stock on hand
- Make part with no BOM, buy part with BOM
- Part status “P” on part master (pre-release)
- Buy part with no where-used
- Multi-location is yes, no multiple location records
- Planning lead time greater than cumulative lead time
- Multi-location is no, multiple location records exist
- No new standards record
- MRP flag should be changed
- Planning BOM with stock
- Planning BOM with parent
- Planning bill component with no parent
- Planning bill component with invalid parent
- Planning bill component with many parents
- Negative lot on hand
- Lot control is yes, no lot records
- Lot control is no, lot records exist
- No activity in six months
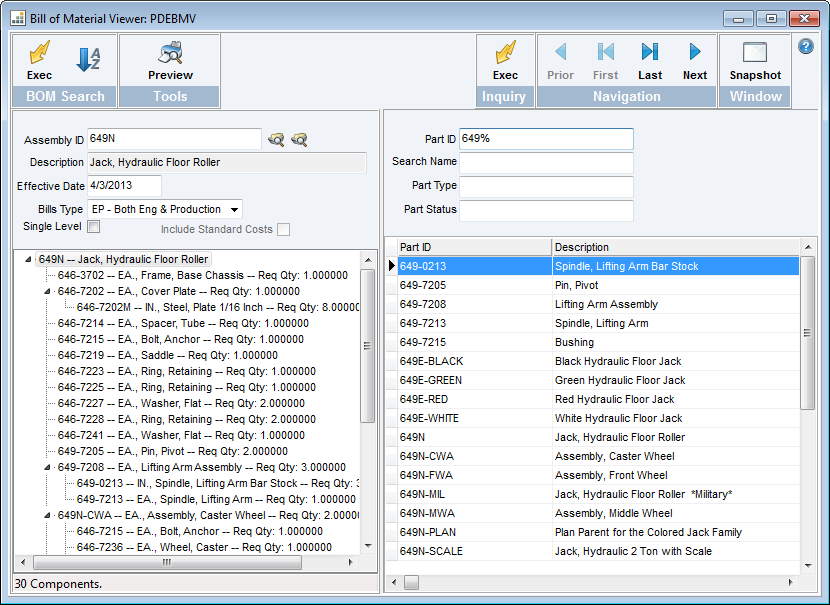
Identify components that make up your top level assemblies using the Bill of Materials Viewer
Real-time Integration
- Inventory Control
- Purchasing
- Job Scheduling/Costing
- Shop Routing
- Materials Management (MRP)
- Master Scheduling